- +371 20 222 809
- Lemorn Tooling OÜ, Estonia, Tallinn, Lasnamäe linnaosa, Majaka tn 26, 11412
- sales@lemorn.eu
UFS Srl. Running to the Top
Website: www.ufs.it
UFS conta ad UFS boasts a hundred personnel, including employees, collaborators and agents, as a family that has (proudly) become extended. The company designs, tests, constructs, tempers and internally coats all of the tools in its 3 operational locations, defined by industrial growth and quality.
Throughout over 70 years in operation, dedicated entirely to the field of thread-cutting tools, UFS has been managed to adapt its resources to the needs of the market through technical, productive and organisational transformations that have led the company to stand strong before major global competitors.
Amplification of production, new research divisions, use of latest-generation computerised systems for order and scheduling management, quality certifications... all represent natural and continuous evolutions for UFS.
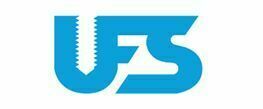
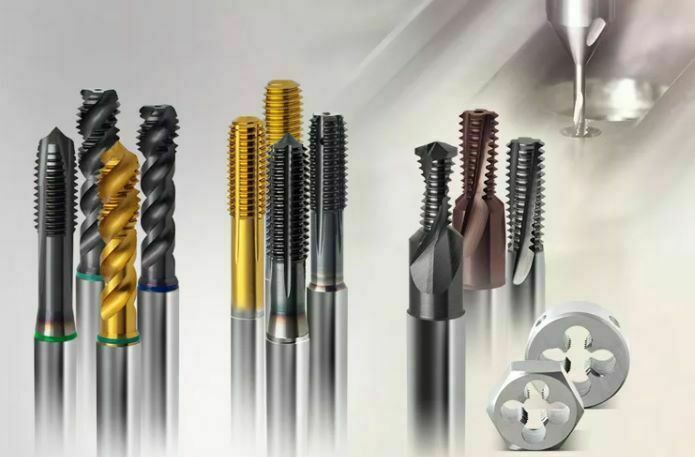
Optimal coordination – in terms of operational and financial management, optimising flows and allowing executive spaces to be created for the introduction of new types of specific tools – satisfies the up-scale processing of challenging and latest-generation materials.
UFS pursues its strong expansion, exports to all European countries (and many non-European countries – particularly in the Asian, South American and North African markets) and the ongoing action of our direct agents, dedicated to foreign markets, consolidating the company’s presence with increasing appreciation.
UFS sells its products in over 40 countries around the world, both through its own sales network and via specialised sales chains (private labels). In Italy, UFS is one of the leading manufacturers of thread-cutting tools, with over 500 clients to whom it provides excellent quality products.
UFS product:
Standard taps, special made-to-design items, and P-NP threaded gauges and dies.
The “standard” UFS tap covers more regular user needs, in compliance with DIN standards. The current catalogue (31-2020) contains over 5,000 products. UFS also produces threading tools upon specific request from the customer. Indeed, the production of this type of tools represents around 30% of company turnover.
UFS tools are divided into 3 product lines, with increasing functional performance and durability to offer the customer the opportunity to achieve better economies of production. There is the LINE range of HSSE steel tools, the PLUS in steels with higher cobalt content and the TOP series representing the spearhead of UFS production with tools designed for machining specific materials.
High strength items for machining materials up to 52 HRC, the taps are in steel that is super-rapid sintered in metallurgy powders with high percentages of vanadium and cobalt, available with surface treatments offering high resistance to wear and oxidation.
Stainless steel is ideal for pieces that are difficult to work and with long chips. The basic steels are HSSV3 type, with 3% vanadium, or steel sintered in metallurgy powders with high vanadium and cobalt content. The cutting geometries and TXC treatment prevent the formation of the built-up edges.
There are light aluminium alloys, long-chip copper alloys and sweet magnetic iron and aluminium alloys with silicon. Items are available with AZ interrupted threads that prevent the formation of the skein shavings with a reduced number of cuts and ample offcut compartments.
In cast iron, the items are made of super-rapid steel sintered in metallurgy powders with a low cutting angle and combined with an accentuated rake angle that render these types of taps suitable for working abrasive materials. They have an increased tolerance of type 6HX and a TiAlN coating, combined with micro surface finishing processes. Also with short intake for tapping with a reduced-dimension or 25° helical discharge chamber for applications on steel cast iron (steel castings).
For titanium, products come in steel sintered in metallurgy powders bearing special cutting geometries. They bear a 15° left helix for through holes and 15° right helix for blind holes. They are also available in 4HX tolerance and with TiCN treatment for processing the most demanding alloys.
For nickel, the pieces have a reinforced body structure. They have a 10° left helix for through-holes and 10° right helix with chip breaker for application on blind holes and also come with a 4HX tolerance and 25° helical taps with rear tapering.
For synchronised rigid tapping, in quality powder-sintered steels, the taps are rebored with h6 shank tolerance to ensure maximum precision at high cutting speed. They can also be used with thermal coil spindles.
Full-thread carbide has straight cuts for machining very abrasive materials. Available with a central hole for the passage of lubricant and with TiCN surface coating.
Thread mould taps in steel sintered in metallurgy powders. The coatings are combined with special surface preparation processes to minimise friction between the tool and material being worked. Available with and without ducts, also with 6HX and 6GX tolerances and an internal lubricant type FOR central hole or with radial FORY-type outputs. There are similarly K-ROLL taps for high-output applications on medium-/high-strength materials.